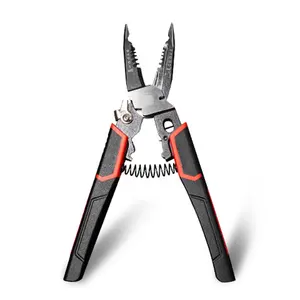
Electrician Special Tool Multi-function Wire Stripper Cutter Pliers Wire Cutter Cutters Wire Stripper Pliers

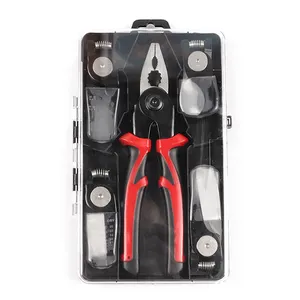
5 In1 Hardware Tools Interchangeable Head Pliers Set Wire Stripper Crimping Plier Cable Shear Scissor Wire Cutter

Safety wire pliers are specialized hand tools designed specifically for the secure installation of safety wire on components and fasteners. Safety wire, also referred to as lock wire or aircraft lock wire, is a pre-formed wire that is wrapped and twisted using pliers to physically join two parts together to prevent unintended loosening or separation due to vibration or other environmental factors. Different from standard pliers or wire cutters, safety wire pliers have a very distinctive form and function tailored for this technical application. They feature offset, curved jaw tips with various serrations and cuts along the inner surfaces. This specialized jaw configuration provides tight gripping power on the fine gauge wires, typically between 18-22 gauge, used for safety wiring. The offset design positions one jaw tip forward to neatly receive the wire as it is wrapped around from the other trailing jaw tip in an unbroken, continuous 360-degree loop. Curved jaws allow the wire to be precisely formed to each fastener without crimping or kinking the wire itself. Deep serrated cuts along the inner edges of the jaws ensure a very controlled, slip-free grip on the wire throughout the entire wrapping process. Available in various sizes to accommodate different wire gauges and wrapping work spaces, safety wire pliers are ergonomically designed with tapered tips, weighted handles, and smooth pivot points and edges for ease of use during repetitive safety wiring operations. Their distinct form exclusively serves this specialized fastening method for securing aircraft, vehicles, vessels, and more.
Safety wire twisting pliers play a crucial job in various industries where unintended loosening of critical components poses serious risks. Their unique application stems from regulations and procedures in fields like aerospace, defense, marine transportation, and others where vibration resistance is paramount. In aircraft maintenance, every fastener, from bulkhead fittings to engine mounts, must be safety wired to maintain torque specifications that ensure airworthiness. This is usually done with aircraft safety wire pliers. Loosening of just a few turns can potentially lead to in-flight component failure. Similarly, naval vessels and defense vehicles rely on safety wires installed with harbor freight safety wire pliers to deter tampering and ensure the functional integrity of moving parts under heavy operation and wave stresses. Beyond compliance, the safety wire provides a visual deterrent against unauthorized access attempts. Its distinctive installation patterns clearly show if tampering has occurred on high-security asset fasteners. This quality also benefits commercial industries like power generation, where loosening turbine blades or engine pieces from use could endanger workers and cause costly downtime.
Advanced engineering and precise manufacturing lend safety wire pliers their specialized characteristics optimized for streamlining secure safety wire installations. At the core, the offset and curved jaw tips facilitate continuous wrapping motions without kinking or crimping defects that could compromise a wrap's integrity over time. Deep serrations cut into the inner curvature of each jaw allow tightly controlled gripping without marring the wire surface. Their elaborate patterned ridges increase coefficients and broadly distribute pressure parallel along wire surfaces for slip-free retention. Contoured indentations in opposing tips neatly pass wire between the plier's mouth. Handles house durable hardened and tempered steel shafts, anchoring robust jaw pivot mechanisms. These bearings withstand the demanding torque stresses of twisting safety wire under tension without binding. Comfortable ergonomic shaping of handles promotes fatigue-free control during lengthy tasks. Balanced weight distribution and elongated tapered shaping of grip ends and jaw tips aid access into recessed areas. Distinct etchings mark tool sizes ensuring the proper pliers are selected corresponding to wire gauges. Protective surface coatings safeguard steel alloys from wear and corrosion, keeping tools primed. Contemporary models take design advancements further. motorized mechanisms auto-twist complete wraps at the push of a trigger, slashing time-consuming manual installations. Advanced alloy selections harden for lifelong precision, twisting countless fasteners across industries. Overall performance backed by serialization confirms guidelines adherence.
Routine care keeps snap-on safety wire pliers performing at optimum standards throughout a lengthy service life spent wrapping thousands of critical fasteners. Before and after each use, cleaning debris from hardened serrations maintains wire gripping power. Gentle solvents dissolve accumulated grease or foreign materials from crevices without compromising surface hardening. Periodic lubrication of moving components like bearing guards against friction and wear. Penetrating oils penetrate confined areas to weatherproof internals from humidity and condensation. Post-application wiping prevents lube accumulation that can attract dirt buildup. Adjustments by certified technicians ensure bearing movement remains smooth. Storage plays a key role; reversible safety wire pliers case interior shelter tools against banging together, which rounds tips. Compartments organized by size maintain traceability and pair pliers to the wires intended. Signs of wear, like deformation, warrant evaluation before risks to wraps can occur. Regularity validates continued conformity with fastener program standards. Replacement timeframes prevent performance lapses, jeopardizing safety compliance. As with any certified aircraft tool, traceable records disclose maintenance history. Compliance relies on traceability, confirming which technicians deployed each tool and for which critical parts. Proper care proves vital in industries where a moment's distraction can endanger many lives.