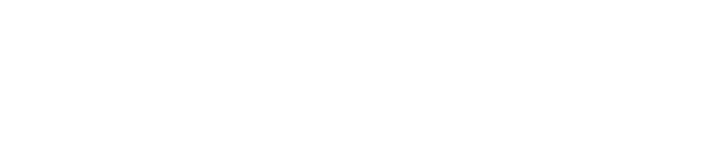
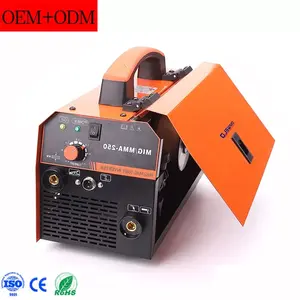
Mini MMA Welding Machine Portable Welder Competitive Prices For Arc Welding Plant Machine For Welding Machine Mig Mag
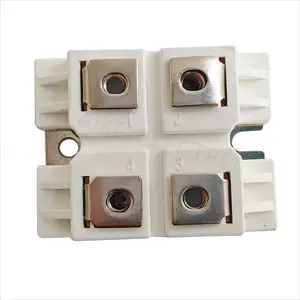
IGBT Module 1200V 100A Single Switch NPT Rugged Type Power Module For Welding Machine And Induction Heating


Professional Factory CE Certified Car Light And Ultrasonic Plastic Welding Machine For Car Tail Light


Tarpaulin Welding Machine PVC Tent Welder Hot Air Seaming Machine


1000C Intermediate Frequency Stabilizer Bar Induction Heating Equipment With Cold Forming Process For Heating


High Frequency Electromagnetic Metal Brazing Welding Soldering Induction Machine (JL-30KW)
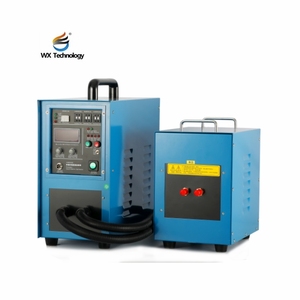
Induction Brazing Equipment Induction Welding Machine

Mosfet ultrahigh frequency induction heating machine copper wire welding machine portable

Power Medium frequency Automatic Induction Stationary Spot Welding Machine For Household Appliance

Saw Blade Diamond Segments Brazing Induction Welding Machine

15KW Compressor Components Braze Induction Welding Machine

Ultrasound Scouring Pad Ultrasonic Long Plastic Parts Auto Hot Melting Oil Booms Induction Heating Welding Machine
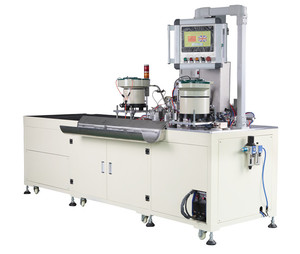
Automatic high effiction induction thermocouple brazing welding machine

Handheld Heater Machine Quenching Welding Equipment Forging Soldering High Frequency Induction Heating Machine

handhold High Frequency Induction Heating Machine Mini-Inductior Welding Machine
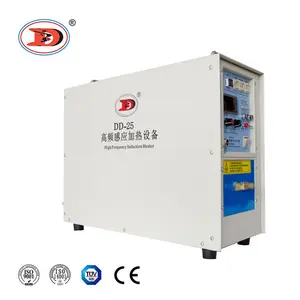
HF Inductive Kaierda Welding Machine
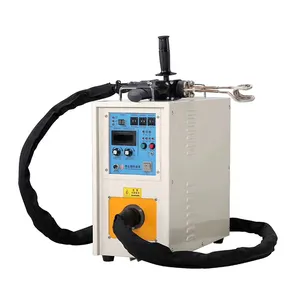
35kw Small High-Frequency Induction Heating Welding Machine For Copper Aluminum Steel Pipe Brazing
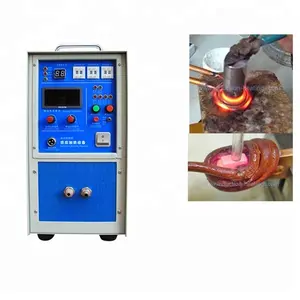
Portable 16kw Supersonic Frequency IGBT Induction Welding Machine
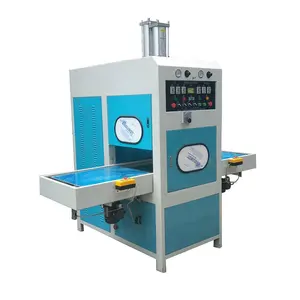
high frequency induction pvc shoes upper welding machine 8kw, push table high frequency plastic welding and cutting machine
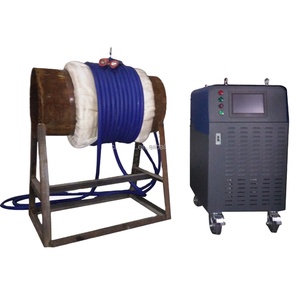
Pro-35 Induction weld preheat PWHT stress relieving heating treatment machine PWHT system P91 pwht machine

25kw 380V 1P High Frequency Induction Heating Welding Machine for Alloy Cutters and Metal tubes
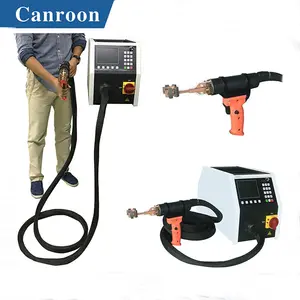
Canroon high frequency portable induction welding machine for steel bar brazing
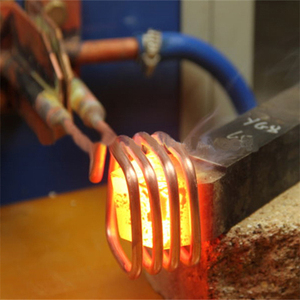
Induction heating welding machine for Alloy copper tube brazing welding
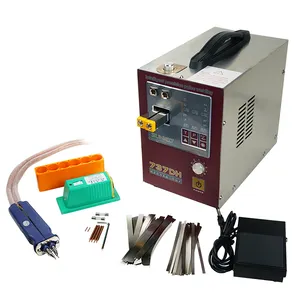
SUNKKO 737DH Spot Welding Machine Induction Delay 4.3KW High Power Automatic Pulse Spot Welding Machine For 18650Battery Welding

High Frequency Electromagnetic Metal Brazing Welding Soldering Induction Machine (LSW-30KW)
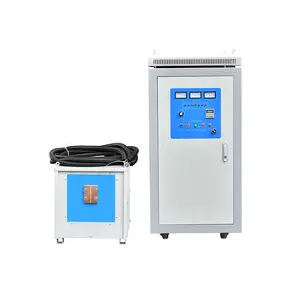
Superaudio Frequency Induction Welding Machine for Diamond Segment Brazing
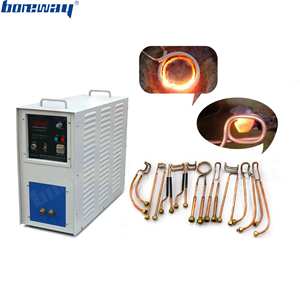
25KW High frequency induction heating welding machine metal welding machine stainless steel welding machine
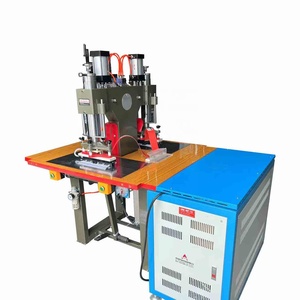
Factory Direct New Double-Headed Pedal High-Frequency Plastic Welding Equipment Automatic Industrial Induction Sealing Machine

6-station induction welding machine

IGBT Induction Portable Aluminum Welding Machine

high frequency induction heating machine plastic welding machine for metal welding to plastic
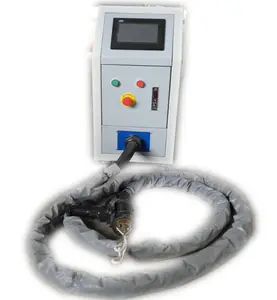
Portable Induction Heating /Brazing machine/Welding machine

New Product 2021 High Frequency Induction Heating Machine TGG-35KW Welding Induction Heating Machine magnetic heater

Preheat & Post weld heating treatment (PWHT) induction machine weld preheat pipe heater

Yongda IGBT 160KW super audio frequency induction brazing/welding/soldering machine

Best Price Induction Post Weld Heat Treatment Machine

High Frequency Spiral Fin Tube Induction welding Machine For steel Pipe tube

China 120KW HF induction heating machine weld heat treatment equipment
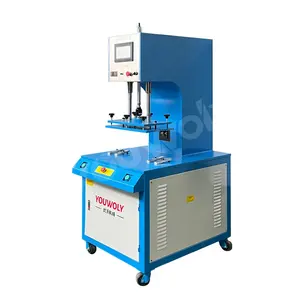